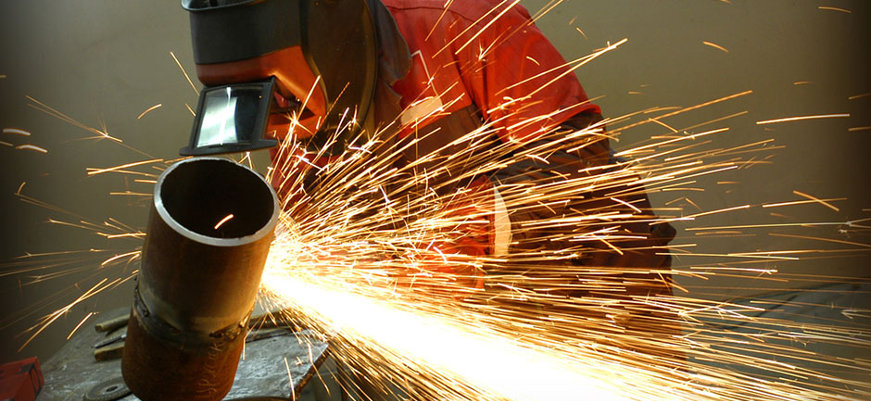
Schneiden von Metallen durch Trennen von Partikeln
Eine der Metallbearbeitungstechniken ist das Scheiden. Das ist ein Vorgang, bei dem das Schneidwerkzeug, das Material durchdringt und dabei Partikel trennt.
Es gibt zwei grundliegenden Möglichkeiten, Metall zu scheiden:
- Grobverarbeitung: stellt die Grundbearbeitung dar und besteht aus Schaben, Bohren, Fräsen usw. Das Hauptziel dieser Art der Verarbeitung ist es, eine größere Menge an Material zu entfernen.
- Schluss- bzw. Endverarbeitung: Zerkleinern und Schleifen. Dieser Vorgang wird nach dem Schneiden durchgeführt.
Wenn das Schneidwerkzeug in Gruppen eingeteilt wurde, könnte sie wie folgt eingeteilt werden:
- Handwerkzeug zum scheiden – dazu zählen die Handsäge und Schere.
- Zerspanungsmaschinen – dazu zählen der Leserschneider, Plasmaschneider, Wasserstrahlschneider, Autogenschneider usw.
Die Entscheidung für die Auswahl der Schneidmethode hängt von der Geschwindigkeit, der Qualität, der Präzision und den allgemeinen Anforderungen für das Schneiden ab. Dementsprechend werden alle Schneidwerkzeuge ausgewählt.
Ein Beispiel für Blech ist das Handschneidwerkzeug.
Für Blech wird normalerweise die Schere verwendet (Hand- oder Tischschere), beim diesen Vorgang resultieren minimalen Graten, wegen den scharfen Kanten muss man das Metall weiterverarbeiten werden. Die Graten treten während des Scheidevorgang auf.
Das maschinelles Schneiden wir meistens mit CNC Technologie (computergestützten Steuerung) hergestellt, was viele Vorteile bietet.
Das CNC- Schneiden von Metallen mittels Laser erreicht z.B., eine Genauigkeit von 0,2 mm. Das Schneiden von Eisen ist auch mit einer CNC und einem Messer (z.B., Plasmaschneider) möglich.
Das Prinzip des Metallschneidens
Beim Schneiden wird das zu schneidende Material ( Blech, Eisen, Stahl..,) plastisch verformt, die Spannung des geschnittenen Materials nimmt zu, es beginnt nachzulassen, was schließlich zu Rissen oder Verformungen führt. Beim Schneiden tritt Graten auf und dann muss man es zusätzlich behandeln. Bei Laserschneiden trifft dies nicht zu.
Schneidwerkzeug
Neben der genannten Aufteilung in Hand- und Zerspannungswerkzeug können Schneidwerkzeug unterteilt werden in:
- Trennwerkzeuge (z.B. Messer)
- Zerspannungswerkzeug (z.B. Bohrer)
- Schmelzschneider (Schneidewerkzeuge ohne direkten Kontakt-Schneiden mit Energie) z.B. Plasmaschneider.
Wie bereits erwähnt, tritt beim Schneiden des Materials Grate auf. Mit einigen Techniken ist die Menge der Grate vernachlässigbar, während in einigen größer.
Die Menge und die Art der Bildung von Graten hängt von den plastischen Eigenschaften des zu schneidenden Materials ab und kann unterteilt werden in:
- Unterbrochener
- Kontinuierliche
- Zusammengesetzt
Beim Schneiden kann es zur Wärme führen die dazu führt das sich das Metall verformt. Dies entsteht wenn die Wärmeenergie zu groß ist.
Die heutigen hochentwickelten Schneidetechniken übertragen jedoch meist nur eine minimale Wärmemenge auf das Material, so das Verformung vermieden werden.
Darüber hinaus hinterlassen die meisten anspruchsvollen Schneidetechniken (Plasma, Laserschneider) nur sehr wenige Grate. Die braucht man nicht zusätzlich bearbeiten.
Durch die CNC Technologie, erhöht sich die Präzision beim Schneiden. Das CNC Schneiden von Metallen mittels Laser erreicht eine Genauigkeit von 0,2mm.
Material für Verarbeitung von Schneidewerkzeug
Beim Schneiden von Material kommt es nicht nur zur Verformung sondern auch zur Abnutzung.
Deshalb hat man folgende Erwartungen auf das Schneidwerkzeug:
Kalteschneide Werkzeuge: bis 200 Grad, muss Widerstandsfähig gegenüber Abnutzung, Stoß/Schlag und Verformung.
Heiße Schneidewerkzeuge: über 200 Grad, Verschleißfestigkeit, Korrosion und Schlag.
Jedes Schneidwerkzeug unterscheidet sich in:
- Ursachen, die den Verschleiß beeinflussen– Wärme kann den Verschleiß erhöhen
- (Kerb-)Verschleiß bzw. Ausgabemechanismen: z.B. Oxydation
- Art und Weise der Abnutzung: z.B, Bruch
- Verschleißkriterien: Verschiedene Schneidstoffe haben unterschiedliche Verschleißkriterien.
Das Schneiden von Metallen ist einer der wichtigsten Prozesse vor der Verarbeitung. Die Entwicklung der CNC- Technologie ermöglichte eine hohe Schnittpräzision von bis zu 0,2mm.